超音波を用いると、ネジや電子部品などの小さなものから自動車や橋のような大きなものまで、あらゆるものを破壊することなく検査することが可能であり、近年ますます利用範囲が拡大している。
伊藤忠テクノソリューションズ株式会社が開発した超音波シミュレータ「ComWAVETM 」は、超音波を用いた非破壊検査・計測の様々な分野で活用されている。
本稿では、超音波シミュレータ「ComWAVETM 」の開発経緯、溶接部検査等への適用、クラウドを利用した非破壊検査シミュレータ構築の説明を通して、「ComWAVETM 」が非破壊検査の効率化および高精度化に貢献することを示す。
超音波シミュレータ「ComWAVETM 」の開発経緯
超音波は、可聴上限周波数2万Hz以上の気体・液体・固体中の振動を指し、人間は音として認識することができないため、騒音となることはない。また、人体に無害とされており、あらゆるものの検査に、安全に使うことが可能である。
しかし、超音波は目に見えないこともあり、非破壊検査で重要となる、「隈なく検査する」ためには、「超音波を可視化」することが非常に重要となる。
超音波シミュレータ「ComWAVETM 」は、この「超音波を可視化」するシミュレータとして開発が開始され、2006年にリリースされた。
しかし、超音波の波長は非常に微小であり、高精度な解析を行うには計算量が膨大となり、そのようなシミュレータは世の中に存在しなかった。
このため、シミュレータの解析を行うソルバの開発のみでなく、モデリングや可視化を行うインタフェイスまで、すべてを自社開発する必要があった。
ソルバには高精度な解析手法として知られている有限要素法を採用し、独自のアルゴリズムにより、これまで不可能であった100億要素規模の大規模な超音波伝搬解析をクラスタPCやGPGPU上で高速に実行できる画期的なシミュレータを開発した。
図1は、実験で超音波を可視化する手法(光弾性法)を用いてガラス中の超音波を可視化した結果および探傷エコーを「ComWAVETM 」の結果と比較したものである。
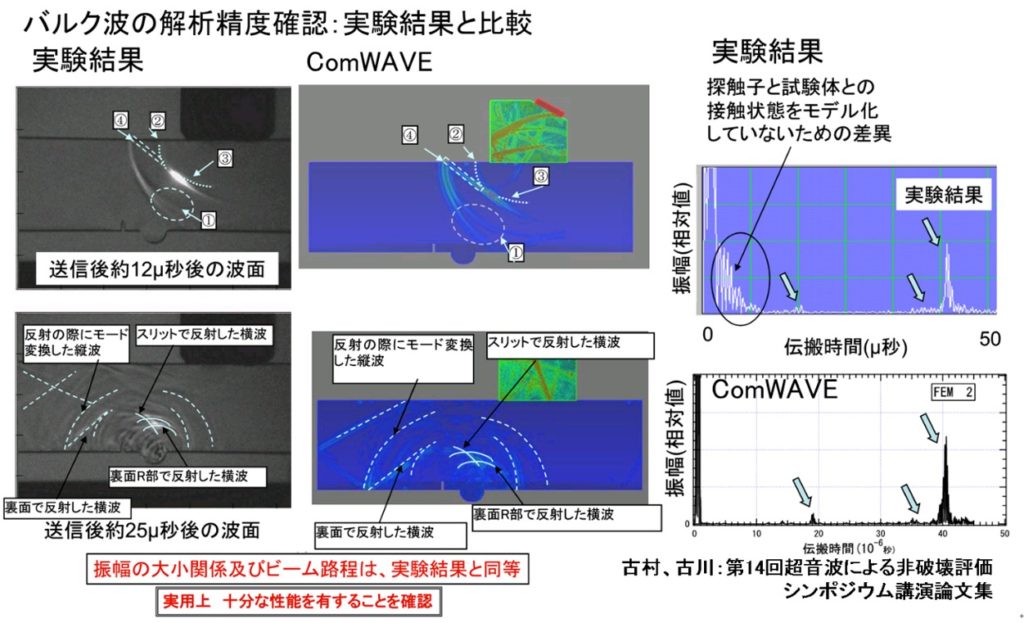
図1 実験から得られた超音波伝搬図および探傷波形と「ComWAVETM 」の比較
超音波伝搬の可視化画像および探傷エコーとも、実験を良く再現していることが確認できる。このように、「ComWAVETM 」を用いると、実験では見ることが困難な、検査体中の超音波を可視化し、容易に探傷エコーの起源等を確認することが可能なため、ノイズやエコー高さの定量評価に有効であり、高精度な検査・計測を行う上で重要なツールであることがわかる。
溶接欠陥の画像化シミュレーション
「ComWAVETM 」には、溶接部探傷試験で得られるA,B,C,Dスコープ画像を再現する機能があるが、画像作成の際に、膨大な計算を高速に行う必要があるため、クラウド環境下での動作が有効である。
また検査を行うスキャン動作に従った解析モデルを自動的に作成し、連続実行を行う機能を開発し、大量の計算を効率よく処理し結果を可視化できる環境を構築した。
本機能を用いると、実際の検査をシミュレータで再現できるため検査員の教育訓練に用いることができるだけでなく、溶接部探傷試験時の余盛エコーを再現させることで、これまでの溶接部探傷試験のみでは困難であった、溶接部欠陥有無の特定をシミュレータを用いることで高精度に検出可能にする等の利用方法が考えられる。
ここで、参考のため、実際の溶接部探傷のB,C,Dスコープ画像を図2に示す 1) 。溶接部余盛は、溶接線方向に不均一のため、C,Dスコープ画像には余盛エコーが不均一に多く存在していることがわかる。
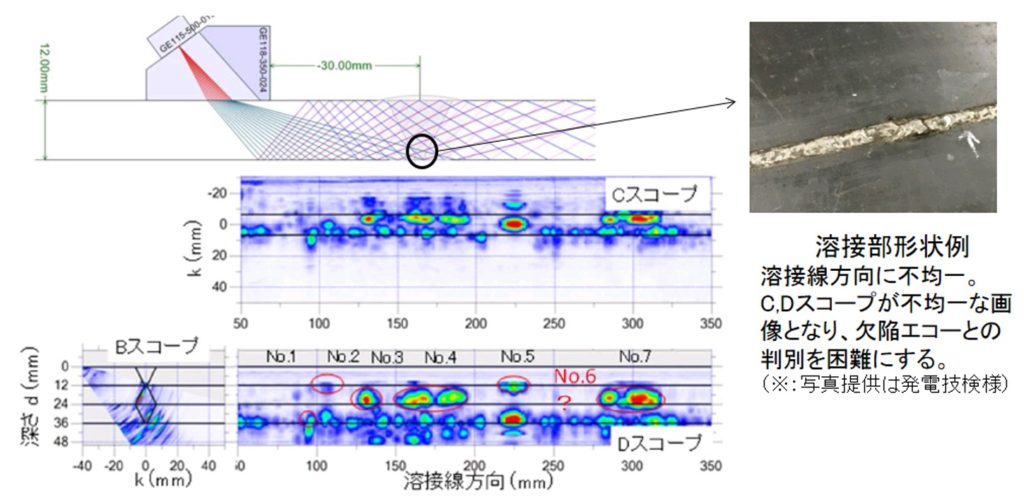
図2 実際の溶接部のB,C,Dスコープ画像例 1)
このことから、これらのエコーの中に欠陥エコーが存在したとしても、判別が困難であることが容易に想像できる。上記のとおり、溶接部余盛を残したままの継手では、余盛から比較的強い超音波エコーが得られることがわかる。
このエコーは疑似エコーと呼ばれており、超音波検査において欠陥有無の判別を困難にしている原因の1つである。
1)「ComWAVETM 」による溶接部疑似エコーの解析
図3は、突合せ鋼溶接部に対してのBスコープ画像のシミュレーション結果である。ここでは、異なる2つの溶接部余盛形状を対象とし、溶接部と母材部の裏面境界に欠陥を設けた場合と設けない場合についてモデル化している。
探傷方法は、2MHz,16chのフェーズドアレイプローブを用いて、横波斜角20~80度のセクタスキャンにより画像化を行っている。図3aおよび図3cは欠陥をモデル化していないため、ここに表れているエコー画像は、溶接部余盛に起因していることが分かる。
なお、このエコーは無欠陥にもかかわらず得られるエコーのため、疑似エコーと呼ばれている。強度は図3aの余盛形状1は強く、図3cの余盛形状2は弱い。これより、余盛エコーの強度は余盛形状に大きく依存することがわかる。
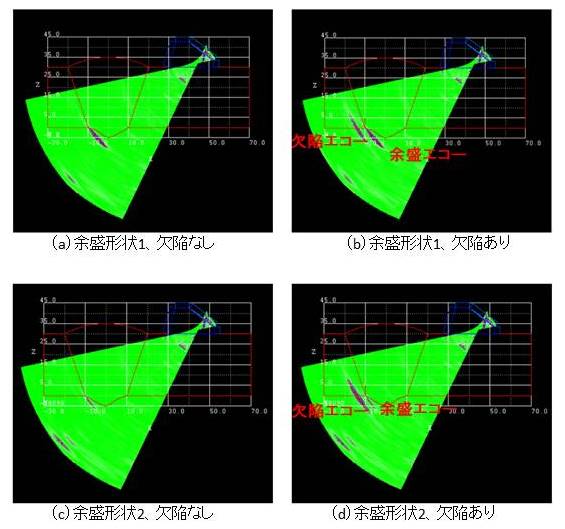
図3 余盛エコーと欠陥エコーの判別が困難なBスコープ画像の解析例
次に、欠陥を入れた際のエコー画像を図3bおよび図3dに示す。
余盛エコーと欠陥エコーの場所は近接しており、強度は図3bでは余盛エコーと欠陥エコーが同レベルの強さであるが、図3dでは余盛エコーはあまり見えず欠陥エコーが強い結果となっている。
これより特に図3dの欠陥エコーと図3aの余盛エコーは強度も位置もほぼ同じとなっており、余盛エコーと欠陥エコーの区別が困難であることがわかる。
なお同図では、余盛エコーと欠陥エコーを欠陥なしのエコー画像との比較により特定している。しかし、実際の探傷試験では、欠陥有無は未知のため、得られたエコー画像のみから、欠陥エコーを判別する必要があり、余盛がある場合の欠陥エコーの特定は一般的に非常に困難であることがわかる。
2)「ComWAVETM 」B,C,Dスコープ画像取得
実際の溶接部には、様々な余盛形状をもつ継手が存在する。これらの検査は先にも述べたように余盛エコーが多く発生し、欠陥有無の判断をきわめて困難にしている。
この課題を解決するために、B,C,Dスコープ画像を得る機能を、超音波シミュレータ「ComWAVETM 」に本年度機能追加中である。
「ComWAVETM 」では、図4に示すように、様々な実際の溶接部をデジタルスキャンや画像取込により読み取り、図4bに示すように3次元モデルを容易に作成することが可能である。
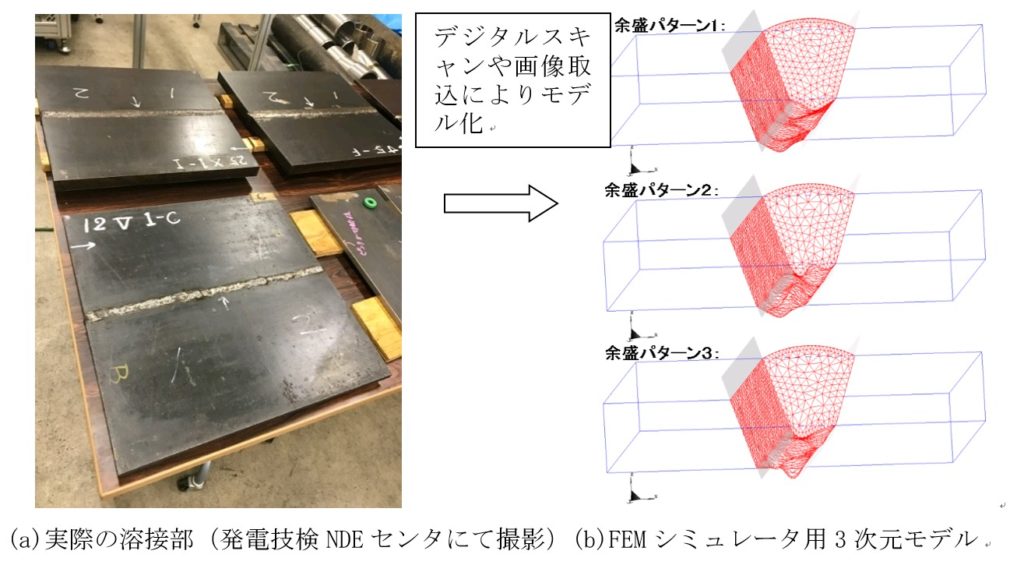
図4 実際の溶接部の超音波シミュレータ用3次元モデル
また、溶接部探傷試験で得られるB,C,Dスコープ画像をシミュレータで得るためには、画像作成の際に、膨大な数の超音波伝搬計算を高速に行う必要がある。たとえば、図2に示すようなB,C,Dスコープ画像の場合、フェーズドアレイのセクタスキャンを溶接線方向に指定したピッチで移動して作成する。
この際、シミュレータでは、溶接線方向に移動するごとにBスコープを計算することになる。ここでは、16chアレイを用いて1mmピッチで溶接線方向1mm~100mmまで移動する場合の計算量について試算する。
溶接線方向1断面のBスコープ計算では、アレイ素子分の16回のFEM超音波伝搬解析が必要になる。また溶接線方向に100ヵ所移動するため、全ケースで 16 × 100 =1,600回のFEM解析(3次元)が必要となる。これをそのまま実行すると、現在の計算環境を用いても、膨大な計算量となり、現実的に不可能である。
図5は、シミュレータを用いてB,C,Dスコープ画像を得るための手順を示した。図5aは探触子を適切に移動させるための条件を決めるための探傷計画策定手順を示している。ここでは、超音波の到達位置を高速に把握できるレイトレース法を用いて、探傷計画を策定している。
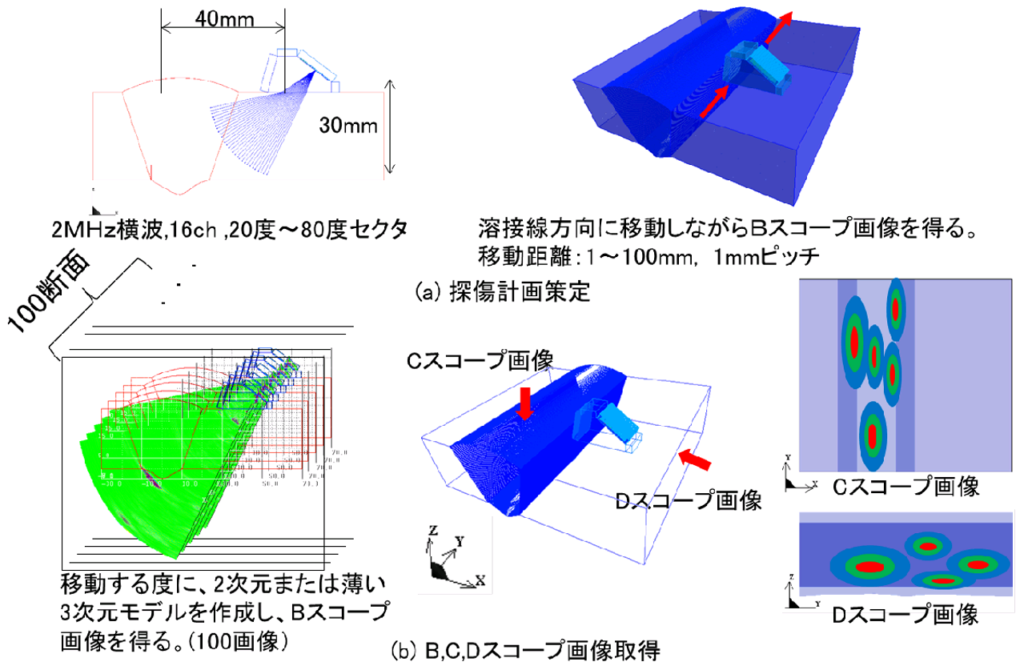
図5 シミュレータによる探傷計画およびB,C,Dスコープ画像取得手順
図5bはB,C,Dスコープ画像取得手順であるが、計算量を削減するために、溶接線方向に移動するたびに、3次元FEM解析を行うのでなく、2次元断面または小規模3次元FEM解析を実施することとした。なお、本計算手法の妥当性評価はすでに古川らの論文 2)に記載されている。
クラウド環境および利用法
1)「ComWAVETM 」のクラウド環境
クラウド環境では、大量のCPUコア数やGPUを容易に利用できるため、このような多数の解析を実行する際の恩恵は大きい。図5の手順でB,C,Dスコープを計算した際に必要な計算時間を、表1にまとめた。クラウド(Rescale)環境でのCPUおよびGPU(K80、V100)を用いた場合について示した。
ここでは、CPUおよびGPUともに、64ケースを1度に実行し、25回順番にJOBを投入し、1,600ケース(64×25)を処理している。その結果、図5のB,C,Dスコープ画像を得るためのデータ取得に、クラウド(Rescale)のCPUを利用すると約10時間、GPU(K80)を利用すると約3時間、GPU(V100)を利用すると約1時間となった。
なおV100はK80よりも新しいGPUであり、K80に比べて計算速度も3倍程度早くなっていることがわかる。表1に示されるとおり、クラウド環境を使えば、大量の計算を同時に実行できるため、B,C,Dスコープ計算を高速実行できることがわかる。
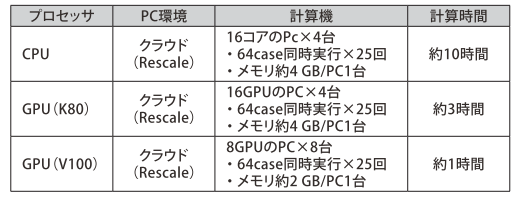
表1 CPUおよびGPUを用いた際の計算時間
なお、今回同時実行ケース数を64としたのは、クラウド(Rescale)では1時間単位の課金となるため、最速計算時間を1時間以上としたためである。クラウド(Rescale)では、さらに多くのコア数やGPU数を同時に利用することもできるため、より高速に計算を行うことも可能である。
2)「ComWAVETM 」のクラウド利用方法
「ComWAVETM 」のクラウド利用方法を図6に示す。モデリングおよび解析結果処理はクライアント側で行うため、クラウドへのJob投入には入力データをアップロードする必要がある。

図6 「ComWAVETM」のクラウド利用方法
また結果はダウンロードすることとなる。この際、複数Jobを実行するバッチファイル作成機能およびデータ圧縮機能を用いて、効率よくクラウド上で計算実行できる環境を構築している。
「ComWAVE Lab for NDE」について
弊社で開発している「ComWAVETM 」は、非破壊検査のみでなく、様々な超音波現象を再現することが可能であり、利用者は多岐にわたる。
このため、非破壊検査に不要な機能等も多く含まれており、非破壊検査技術者が利用するには、煩雑な面もある。そこで、超音波探傷試験をシミュレーションする機能に絞り込み、操作性を向上させたインタフェイス「ComWAVE Lab for NDE」を開発している。
【「ComWAVE Lab for NDE」の特長】
1. 探傷技試験技術者に直観的な操作環境を用意1画面で探傷計画策定から結果の確認までを行えるGUIとした。
2. 探傷計画策定では、レイトレース法により高速に適切なプローブ配置を決定
3. 探傷装置と同様な出力 A,B,C,Dスキャンなど探傷装置と同様な出力を可能とした。
4. クラウドを介した計算やデータへのアクセスを可能とし、B,C,Dスコープ計算等の大量の計算に対応
5. マニュアルレスを実現(アイコン上にマウスを置くと、ヘルプを参照可能)
6. 入出力ファイルは本体のComWAVETM と完全互換(より高度な解析はComWAVETM 本体で実行可能)
FEM 超音波シミュレータ「ComWAVETM 」の活用方法
実際の溶接部では余盛部からのエコーが多く存在し、欠陥有無の判定か困難になることを述べてきた。また、シミュレータを用いると、これらの余盛エコーや欠陥エコーを精度よく再現できることも確認されている 2) 。
このため様々な欠陥や余盛などを高精度に模擬した探傷シミュレータとして、検査員の教育訓練での活用が期待されている。 さらに、FEMシミュレータの活用方法として、上山らの提案している、溶接部欠陥判定手法 2) について述べる。概要を図7に示すが、手順は以下のとおりである。
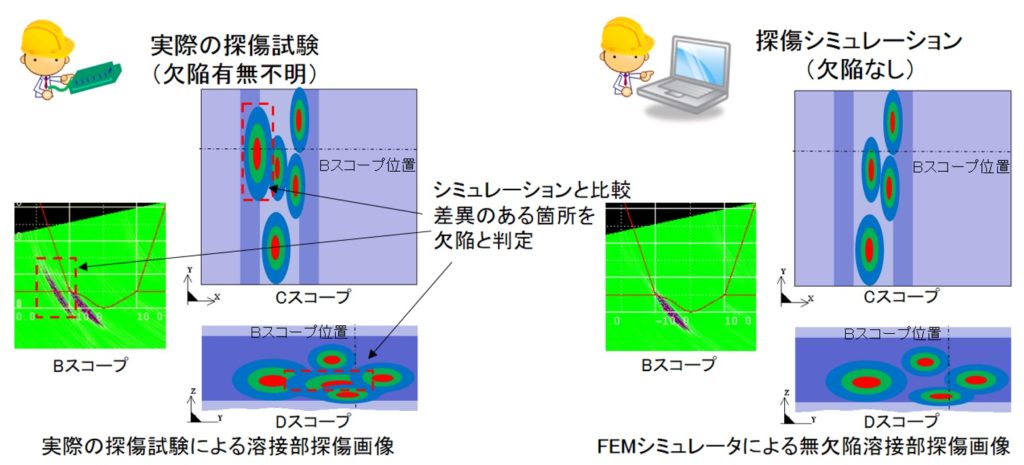
図7 FEMシミュレータの活用例:溶接部の欠陥有無判定
【FEMシミュレータを用いた溶接部欠陥判定手法】
1. シミュレータを用いて、余盛を含む溶接部外形をモデルに取込み、無欠陥溶接部のB,C,Dスコープ画像を得る。
2. 実際の溶接部探傷試験で得られた B,C,D スコープ画像と比較する。
3. 2の比較によりシミュレーションで得られた画像と差異のある部分を欠陥と判定する。
まとめおよび今後の展望
クラウド上で動作し、溶接部探傷試験を容易にする FEM 超音波シミュレータ「ComWAVETM 」クラウドを開発した。出力は実験と同様なA,B,C,Dスコープに対応し、クラウド環境を通して、大量の計算を効率よく実行できる環境とした。
その結果、本シミュレータを用いると、検査員の教育訓練での活用ばかりでなく、溶接部探傷試験で欠陥有無の判定を困難にする余盛エコーをシミュレータにより特定することが可能となり、欠陥有無の判定に貢献することを示した。
また、今後クラウド環境での利用が進むと、シミュレーションデータばかりでなく、実験データについてもクラウド上に置くことが可能になる。これより、図8に示すとおり、探傷試験時に容易にこれらのデータの活用が行えるようになり、メリットが大きい。活用方法および実施手順を同図に示した。
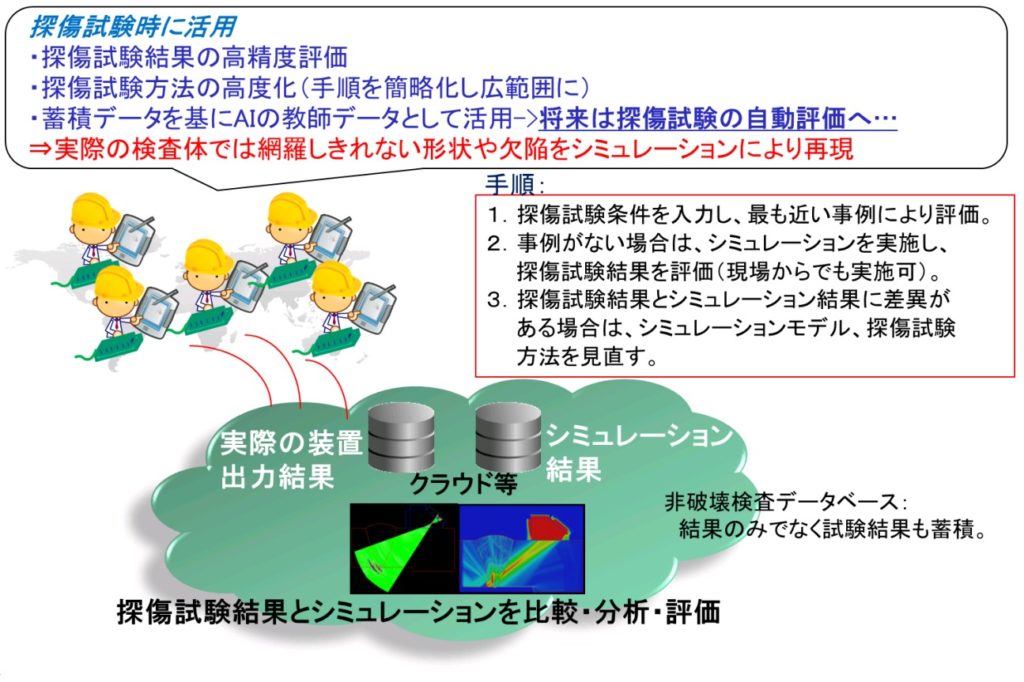
図8 探傷試験時の非破壊検査データベースの活用構想
弊社では、このような非破壊検査の高精度化および効率化に直接貢献できるシミュレータの開発に注力している。これより超音波シミュレータをあらゆる検査・計測分野で活用し、高品質なものづくりや、社会の安心・安全に貢献していきたいと考えている。
■ 参考文献
1) 上山、古川・フェーズドアレイ法と従来法による溶接部の超音波探傷試験結果の比較・非破壊検査協会平成27年度秋季大会講演概要集 (2017).
2) 上山、古川・超音波フェーズドアレイ法の探傷条件設計における超音波探傷シミュレーションの活用・溶接・非破壊検査技術センター技術レビューVol.13(2017).
■問い合わせ
伊藤忠テクノソリューションズ株式会社
TEL:03-6203-7344
E-mail:comwave@ctc-g.co.jp
http://www.engineering-eye.com/ComWAVE/
コメントを残す