キヤノンは、製造業の生産ラインにおける部品供給の自動化を図るシステムとして、バラバラに山積みされた部品の位置・姿勢を高速・高精度に3次元認識することを特徴とした3DマシンビジョンシステムRVシリーズにより、マシンビジョン市場に参入した。
累計約100セットを出荷し、最近になって、量産工場での複数使用も進んできた。本稿では、実際の利用時にポイントとなる機能を中心にRVシリーズを紹介する。
1.はじめに
製造業の生産ラインにおいて、バラバラに山積み(以下、バラ積み)された状態の部品をロボットでピックアップし、次工程に渡す自動化が着目されている。
これは、多くの自動化された製造装置において、部品が整列されて供給される必要がある一方で、個々の部品は他工場、他工程で製造され一旦輸送等においてバラ積み状態となることが多いために、供給部分に関しての自動化が進んでいないためである。
ボウルフィーダ等のパーツフィーダを利用できる場合もあるものの、大きな部品には適用できない、個別の部品形状に合わせた作り込みと調整が必要、部品が詰まって止まってしまうなどの課題も多く、適用できないことが多い。
この課題に対して、キヤノンは、バラ積み部品の3次元位置・姿勢認識を特徴とする3DマシンビジョンシステムRVシリーズ 1) により市場参入した。2014年4月に最初の製品RV1100を発売した後、より小型ワークに対応するバリエーションモデルRV500、RV300を追加し、累計約100セットを出荷してきた。
最近になって、量産工場での複数使用も進んできた。本稿では、RVシリーズの特長について、実際の利用時にポイントとなる機能の説明も交えて紹介する。
2.製品構成と基本となる技術的特長
RVシリーズは、パターンを投影し画像を取得する3Dセンシングを行う3Dマシンビジョンヘッド部と、PC上で動作する3D認識ソフトウェアからなる。
RVシリーズには、計測範囲の異なる3つのモデルがあり、対象とするワークの大きさにより最適なモデルを選択することとなる。図1は、計測範囲540×540 × 200mmのモデルであるRV500をロボットアームとともに設置した例である。
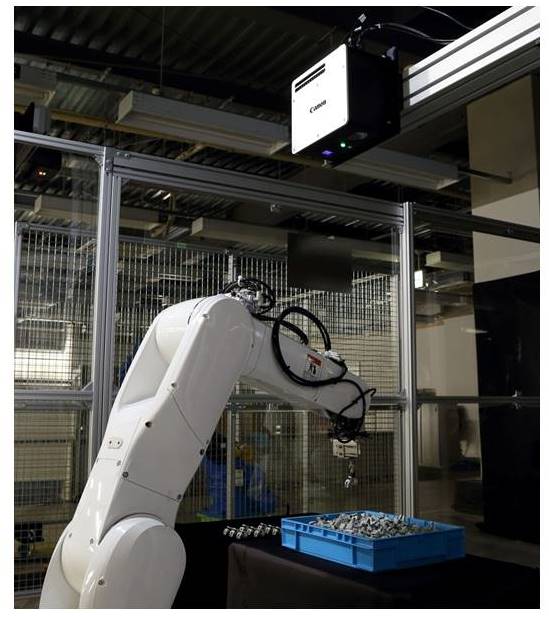
図1 3DマシンビジョンシステムRV500設置例
このように、3Dビジョンシステムは、ワークを積載したパレット(下部の箱)の上方に設置して利用する。ロボットから計測要求を基に計測し、3D認識結果をロボットに返し、ロボットがピックアップ動作をするという使われ方となる。
2.1 基本的な処理フロー
RVシリーズがバラ積みにてワークを認識する基本的は処理フローを図2に示す。この図にあるように、基本的な処理フローは、次の4つの処理工程からなる。
① 複数種類のパターンを投影し、バラ積み部品の距離点群データを計測する。
② バラ積みの中から、部品を検出する。
③ 3DCADモデルを用いて、部品の精密な3次元位置・姿勢を求める。
④ ロボットハンドが部品をピックする過程で、周囲に干渉することなく把持可能か判定する。
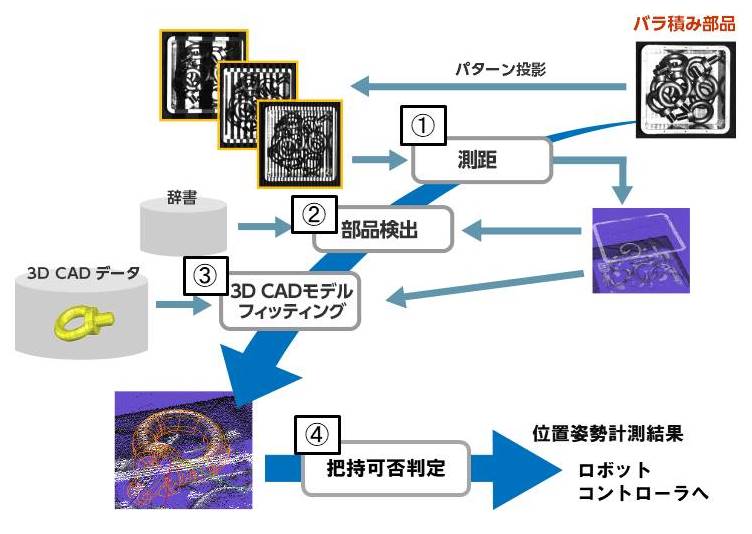
図2 基本的な処理フロー
市販されている3Dビジョン製品には、①の3次元距離点群の計測のみが用意されていて、②以降の認識処理に関しては、個別システムごとに作り込むことを前提とし、機能が用意されていない製品も多い。
しかしながら、点群計測とは、2Dビジョンにおける濃淡画像の取得の段階に相当するものであり、その入力を基にしたワークの認識機能こそ3Dビジョンとして重要な機能である。
キヤノンのRVシリーズでは、②と③からなるワークを認識する機能、および④のロボットで把持可能か否かを判定する機能を提供することで、ビジョンにかかわる特別な知識やスキルを必要とせず、システム構築を行うことを可能としている。
2.2 認識のための独自技術
前節で述べた処理フローの中の②と③とが、ワークを認識する基本機能である。キヤノンでは、この2つの工程からなる認識処理それぞれに対して、多様な対象に汎用的に利用できる独自方式を開発し、製品に盛り込んでいる。
まず、②の工程は、バラ積み状態から、部品がどこにあるのか、その大凡の位置・姿勢とともに部品を検出する機能である。これには、3次元姿勢を離散化して数千からなる多クラスとし、ワークの存在位置を探すのと同時にどのクラスに分類されるのかを高速に演算する方式を開発し、採用している。
この多クラス分類のために、事前にCGを用いてワークの全方位からの「見え」を生成の上で学習する方式となっている。次の③の工程は、正確なワークの位置姿勢を求めるための処理であり、3D CAD モデルを計測データにフィッティングすることで実現する。
②で得られる概略位置姿勢を初期値として、距離点群と濃淡画像から得られるエッジの両方を同時に用いるための様々な工夫を盛り込んだ独自の方式でフィッティングを行う。
この2つの処理工程によって、部品を認識するためのプログラミングは必要ではなく、3D CADモデルの準備と簡単な事前撮影だけで認識処理のセットアップを可能としている。
3.様々な状況への対応力
前章では、RVシリーズの基本的な構成と特長について述べたが、実際の工程に適用するにあたっては、様々な状況が起こりうる。ここでは、頻繁に起こる状況に照らし合わせて、実際の利用場面で適用する際にポイントとなるRVシリーズの機能について述べる。
3.1 似て非なる姿勢への誤認識の排除
工業部品には、概ね対称的で細部のみが異なるような構造をもつものが多い(図3)。図3aは、中心の軸を基準として概ね回転対象の構造であるワークの例である。
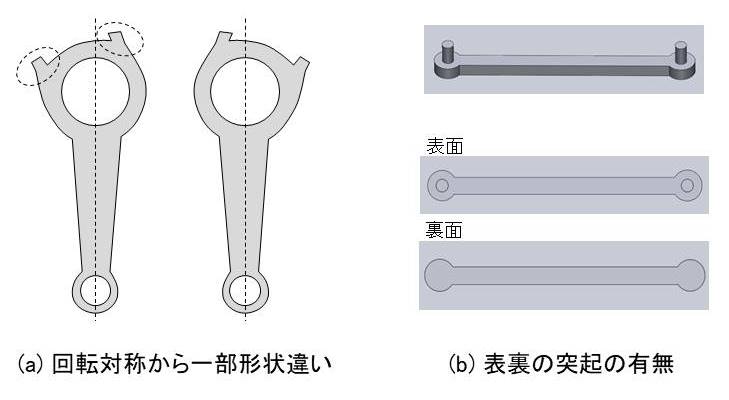
図3 誤り易い姿勢
人が見ると楕円で印した部位に差があることはすぐにわかるものの、構造全体から見ると局所的な領域に過ぎないため、バラ積み状況下での姿勢認識においてはこの2つの姿勢間で誤認識する場合がある。
また、図3bは、表裏の一面にのみ突起物があるようなワークである。この場合も、表裏ほぼ同じ見た目となるケースが起こりうる。 RVシリーズでは、このような概ね対称的な構造をもつことから生じる誤認識を排除するため、以下の2段階機能をもつ。
(1)見かけ上類似する姿勢を事前に登録し、「誤りやすい姿勢」として特別に比較する機能
(2)誤りやすい姿勢間での比較において、特に比較する局所的な部位の指定機能
(1)は、見かけ上類似する姿勢をCG描画されたGUI操作画面にて、誤りやすい姿勢として登録し、後処理で誤認識を判定する機能である。具体的には、2.1節で述べた②と③からなるワーク認識をした後に、得られた姿勢を基準として、誤りやすい姿勢を加味した新たな候補姿勢を生成し、計測値との誤差が小さい方を出力する機能である。
(2)はさらに、区別がより難しい場合に、誤りやすい姿勢間を比較するときの比較部位を局所的に指定する機能である。 実際の工程において、本機能を用いるケースは少なくない。実用性を高めるためにキーとなっている機能の1つである。
3.2 パレットの入れ替えダウンタイムの解消
バラ積み部品のピッキングを行う処理において、パレットに積載されたワークをピッキングしていくと、いずれは空となる。その後にワークが積載されたパレットに入れ替える際に、工程が止まってしまうダウンタイムが発生する。このダウンタイムを最小化するために、パレットの置く位置を複数箇所とし、その上方からそれぞれ計測できる機能を提供している。
具体的には、後述する3Dマシンビジョンヘッドのコンパクトさを活かし、1軸スライダに搭載可能とするケーブルを用いた上で、複数位置から計測をシームレスに設定できる機能をオプションソフトウェアとして提供している。事前に複数地点にてロボットとビジョン間の配置キャリブレーションを行うことで利用可能となる。
3.3 ワークの部分的な認識
構造上変形が生じやすいワークであるため、変形しにくい特定の部位のみで認識したい場合や、計測範囲よりも大きなワークを認識したい場合に、ワークの部分的な形状を入力することで認識可能とする機能を提供している。
図4は、RV1100(計測範囲:1,160×1,160×600mm)を用いたとしても、ワークが視野からはみ出してしまう例であり、ワークの部分的な領域のみで認識している例である(オレンジ色が登録した部位)。
.png)
図4 ワークの部分形状による認識
なお、部分的に認識させたい部位として複数指定することも可能であるため、視野に入る部位が唯一の特定箇所である必要はない。たとえば、長尺物の両端部をそれぞれ登録することも可能である。
また、ワークの全体形状を表す3D CADの登録は別途行うことができ、把持情報の登録等は全体形状に対して実施することとなるため、認識に用いる部位を局所的にすること以外に関しては、全体形状での通常の認識の場合と同じ設定を踏襲して実施することが可能である。
3.4 複数のパレットの同時配置
ピッキング用途によっては、多種の部品を同時に扱いたい場合がある。その場合には、複数種のワークをそれぞれ別のパレットに分けて積載し、複数のパレットを計測範囲に配置することで認識することができる(図5a)。
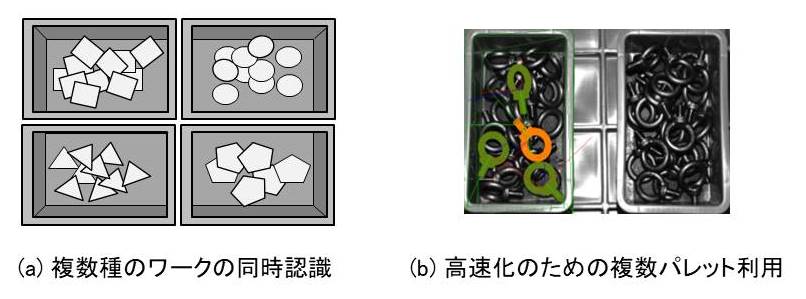
図5 複数パレットの利用
このとき、複数種ワークの素材が概ね同一で、点群データ計測のための露光設定が共通となっていることが条件となるが、図2の①のパターン投影と測距までを1回のみ行い、②以降の認識処理を複数のパレットにわたって実行することが可能である。
この機能の別の利用形態として、図5bに示すように同じワークを複数のパレットに入れて認識することで高速化を図ることができる。パターン投影と測距までは1回で済むことから、RV500、RV300の場合で、1ワークのあたりの認識時間を1.8秒から1.2秒に短縮することが可能となる。
3.5 パターン投影を省略する連続認識
3.4節で述べた複数のパレットを用いるアプローチにおいて、パターン投影と測距1回に対して、それ以降の認識処理を複数回実行しピッキングすることができる理由は、物理的なパレットによってワークが分離されているために、ピッキングによるバラ積みの崩れが他のパレットにまで影響することがないためである。
言い換えれば、ピッキングによるバラ積みの崩れ方が軽微な場合には、パレットが1つであっても、測距結果を何回ものピッキングにわたって利用することが可能であることを意味する。
これを実現するために、ワークをピッキング後に、少ないパターン投影回数でバラ積みの状況が変化したか否かだけ判定し、通常必要な測距のためのパターン投影を省略することで高速化を図る機能を提供している。パレットに対してワークが小さい場合には、連続認識できる回数が大きくなり、大幅な高速化が実現できる場合がある。
4.ユーザビリティ~簡易な認識設定と詳細な変更の両立~
2章にて説明したとおり、RVシリーズでは、部品を認識するためのプログラミングは一切必要なく、3D CADモデルを基にした各種GUIによる設定のみで部品認識設定を完了することができる。
図6は、認識設定をテストするGUI画面の1つで、ワーク認識のテストを実行する画面である。この画面にあるように、利用したい機能の選択を行う必要はあるが、基本的に、それに基づき設定は自動的に行われる。
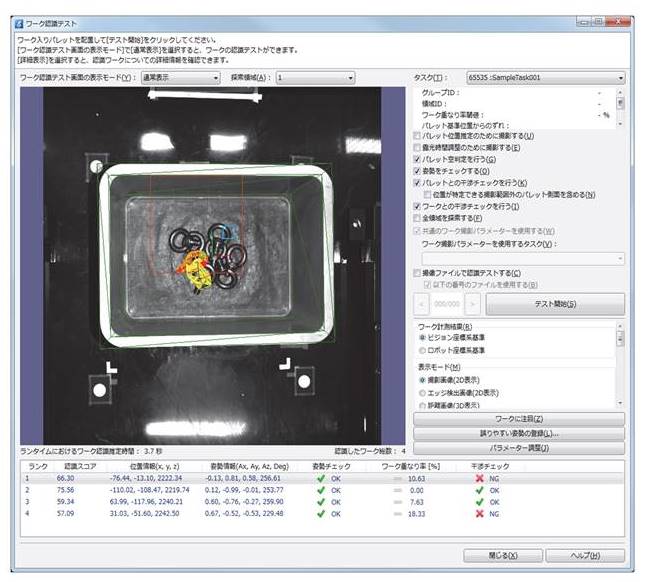
図6 ワーク認識テスト画面
そのとき、認識過程で内部的に必要となる各種パラメータも自動的に設定される設計となっている。この設定の容易性に関しては、実際にロボットとセットでシステム構築をされる多くのユーザから評価をいただいており、優れたユーザビリティを備える。
さらに、最新のソフトウェアVer.1.3においては、認識過程を9つのステップに分け、それぞれのステップで用いるパラメータをエディットできる詳細設定機能を用意している(図7)。
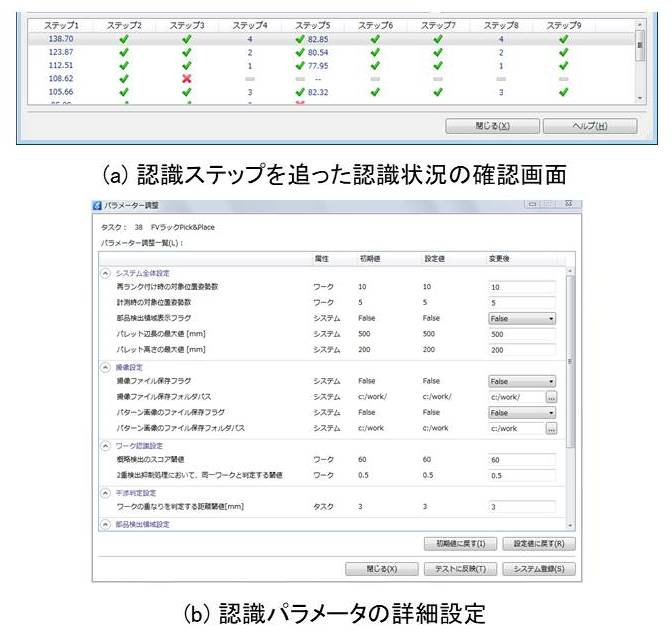
図7 認識パラメータの詳細チューニング
これにより、簡便で使いやすい操作系を維持したまま、知見のあるユーザにおいては、詳細な設定をすることでさらなる認識性能の向上を図ることも可能となっている。
5.設置容易性とメンテナンスフリー
図1の設置例に示したとおり、われわれの3Dマシンビジョンヘッドは、パターンを投影するプロジェクタと撮像センサが一体化された構造である。パレットの上部に設置すればよいだけであり、難しい調整は必要としない。
また、軽量、コンパクトサイズのため、生産ラインの変更や移動に伴う移設にも手間がかからない。防塵・防水、メンテナンスフリーであり、設置後の取り扱いも簡便である。
6.グローバル対応
RVシリーズは、日本のみならず、EU/EFTA、USA、韓国、中国の各国の法規制に対応しており、ワールドワイドで利用可能である(表1)。日本にて構築したピッキングシステムをそのまま海外の工場へ展開することも容易にできる。また、その際には、各国のキヤノンの拠点にてサポート可能である。
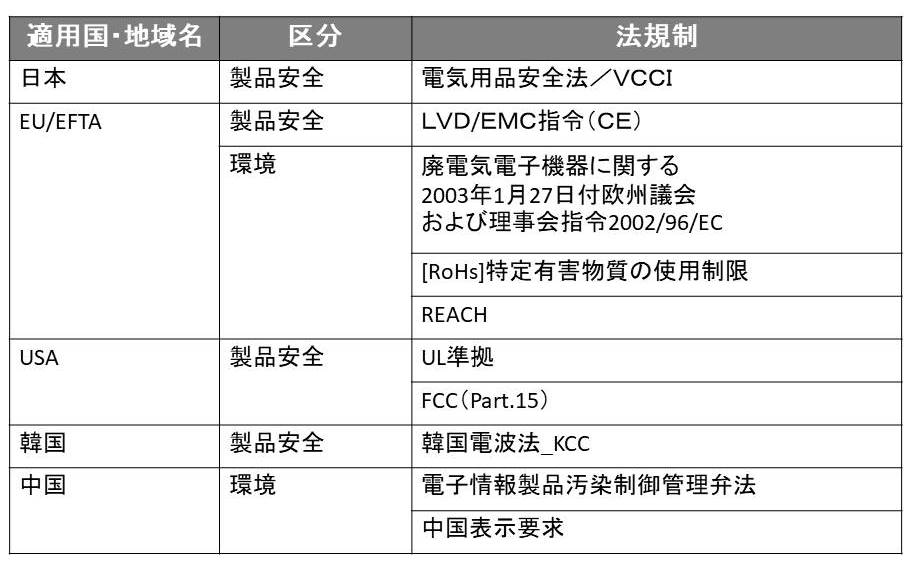
表1 各国法規制対応
7.おわりに
本稿では、実際の生産工程にRVシリーズを適用する場合に有用な機能の説明を中心にして、製品の特長について紹介した。
本製品を利用することにより、現在、人手に頼っている多くの部品供給工程を自動化することができ、工場の生産性を大幅に向上できる。バラ積み供給部の自動化でお困りの際には、是非、問い合わせいただきたい。
■ 参考資料
1)https://cweb.canon.jp/machinevision
■問い合わせ
キヤノンマーケティングジャパン株式会社
産業機器販売事業部
生産革新機器営業部 販売課
TEL:03-3740-3399
https://cweb.canon.jp/machinevision
コメントを残す